Home » Recycling of processing fluids and oils (hydraulic oil, processing oil and processing emulsion)
Home »
We can provide customers with filtration of process fluids such as cutting oils or cutting emulsions in cooperation with a specialist tribotechnical and tribodiagnostic company.
Recycling of processing fluids and oils (hydraulic oil, processing oil and processing emulsion)
- hydraulic oil, process oil and process emulsion
In cooperation with a specialized company Filter Technik Slovakia, s.r.o. focused on tribotechnology and tribodiagnostic, our company is able to provide customers with:
- consultancy in the field of tribotechnics and filtration of process cutting fluids
- performing physicochemical analyses of process liquids and oils and expertise
- filtration of process oils and emulsions – removal of solid mechanical contaminants (chips, abrasives , dust particles, fibres, among others) and soft sludge up to 1 micron absolute size
- choose a suitable filtration technology for your industrial production
- recovery of oils for further primary or secondary use – R9
Advantages of process fluid recycling:
- Reducing the cost of maintaining machinery in the production plant
- Reduction of costs related to established downtime of machinery in production
- Reduction of costs related to the remediation of a potential equipment failure that may occur if the real condition of the cutting fluid quality is not monitored
- Reduction of the required volume of cutting fluids
- Reduction of costs in terms of minimizing the purchase of liquids, which must be continuously replenished in production
- The service life and functionality of machinery in production is extended
- It reduces the financial costs to the customer that he would otherwise have to spend on the disposal of the generated production waste
Process cutting fluids such as process oil or emulsion get various impurities during machining, which can only be removed by perfect filtration and purification of these fluids.
During metalworking operations, there is a relatively enormous loss of cutting fluids (whether oils and/or emulsions) due to sputtering, evaporation, and carryover on the chips. This decrease can represent 7 to 10 % for aqueous solutions, 4 to 8 % for process emulsions and 0.4 to 0.8 % for process oils per working shift. Aqueous solutions and emulsions require the most frequent replacement. Perfect cleaning is required especially when grinding. By continuously replenishing the cutting fluid, the cutting fluid is continuously renewed. Of course, the loss of fluids must be replaced by the addition of a significant amount of process fluids, which represents a financial cost to the customer. The total costs associated with cutting fluids represent an estimated 10-20 % of the total production costs.
Liquid recycling is therefore undoubtedly a cost-effective and ergonomically cost-effective solution. The cleaned cutting fluids can then be returned to production. Great emphasis is required on the constant care of cutting fluids and their regular care.
One way to properly care for and treat cutting fluids is to provide so-called. “Fluid management”, i.e. setting the necessary rules regarding the correct choice of fluids, checking the suitability of their application, quality control, their necessary maintenance, as well as the recycling of these cutting fluids itself.
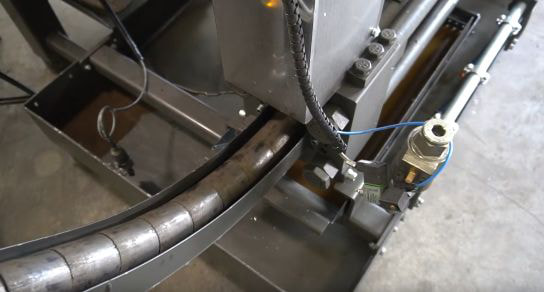
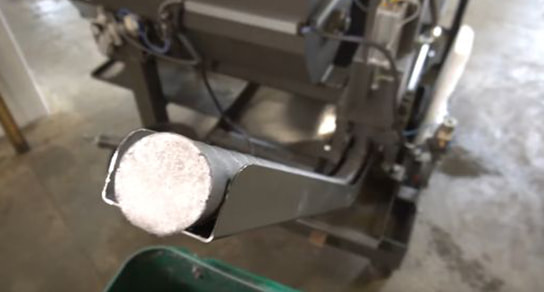



